Generator sets, commonly known as gensets, play a critical role in providing backup power solutions across various industries, from construction to healthcare and beyond.
A key component in maintaining the optimal performance and longevity of these generator sets is the air filter. This seemingly mundane part is crucial in ensuring the efficiency, reliability, and durability of gensets, and understanding its importance can lead to significant operational benefits.
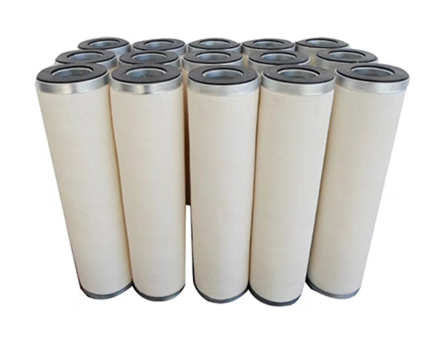
Air filters are vital for protecting the engine of a generator from the ingress of airborne particles, which can include dust, dirt, pollen, or other contaminants. When these particles enter the engine, they can lead to abrasion and wear on moving parts, potentially causing significant damage and reducing the lifespan of the generator. A superior air filter can effectively mitigate this risk, ensuring that the air entering the engine is as clean as possible and maintaining optimal engine performance.
Experts in the field of engine maintenance assert that regular inspection and timely replacement of air filters are foundational practices for preserving generator functionality. Ensuring the air filter is in good condition will help maintain the efficiency of fuel consumption, which directly translates to cost savings. A clogged or dirty air filter can restrict airflow, leading to an imbalanced fuel-to-air ratio. This imbalance can cause fuel to burn inefficiently, increasing fuel consumption and potentially leading to incomplete combustion and excess emissions.
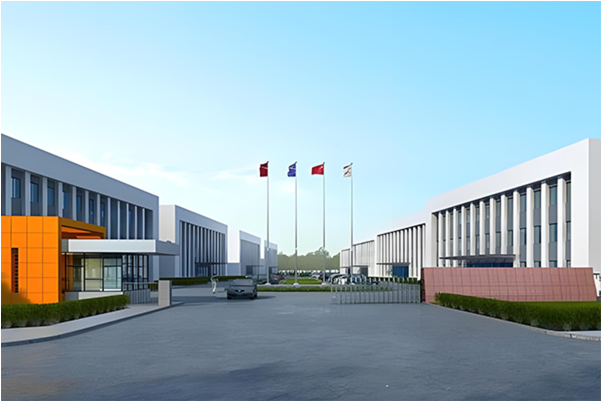
In addition to improving fuel efficiency, a well-maintained air filter supports enhanced overall engine performance. Clean air is critical for combustion, and any compromise in air quality can result in inadequate engine function. This is particularly important in environments with high dust levels, such as construction sites, where the air filter needs frequent checking and possibly more regular replacement to cope with harsher operational conditions.
generator sets air filter
Deploying the right type of air filter tailored to the specific needs of the generator set is a crucial consideration. Not all filters are created equal, and selecting a filter that matches the environmental and operational demands of the generator’s usage can extend the generator's service intervals and reduce maintenance costs. The use of genuine manufacturer-recommended air filters is often advised, as these are typically engineered to fit the generator’s specifications and operational requirements, providing optimal protection and performance.
The authority in generator maintenance, reflected in adherence to manufacturer guidelines for air filter maintenance and replacement, not only bolsters the reliability of generators but also supports compliance with regulatory standards on emissions and efficiency. Operators and maintenance teams need to be proficient in recognizing signs of filter degradation, such as unusual engine noises, decreased performance, or visible smoke, which may indicate the need for immediate filter inspection and maintenance.
Building trust with stakeholders through the implementation of robust maintenance practices around air filters can significantly reduce downtime, increase the reliability of power supply, and provide peace of mind in critical operations, where uninterrupted power is non-negotiable. Establishing a routine maintenance schedule that includes air filter checks can help preempt problems before they impact generator operation, thus ensuring seamless performance in emergencies or peak demand periods.
In conclusion, the humble air filter holds a pivotal role in generator set performance, presenting an intersection of experience, expertise, authoritativeness, and trustworthiness. Through careful selection, regular maintenance, and adherence to expert guidelines, operators can maximize the efficiency and lifespan of their gensets, ensuring they remain a dependable source of power whenever needed.