Innovative solutions in filtration technology continue to redefine industrial efficiency, and wire mesh filter elements stand at the forefront of this advancement. These elements, celebrated for their durability and versatility, have become indispensable in a variety of sectors including petrochemical, pharmaceutical, automotive, and food and beverage industries.
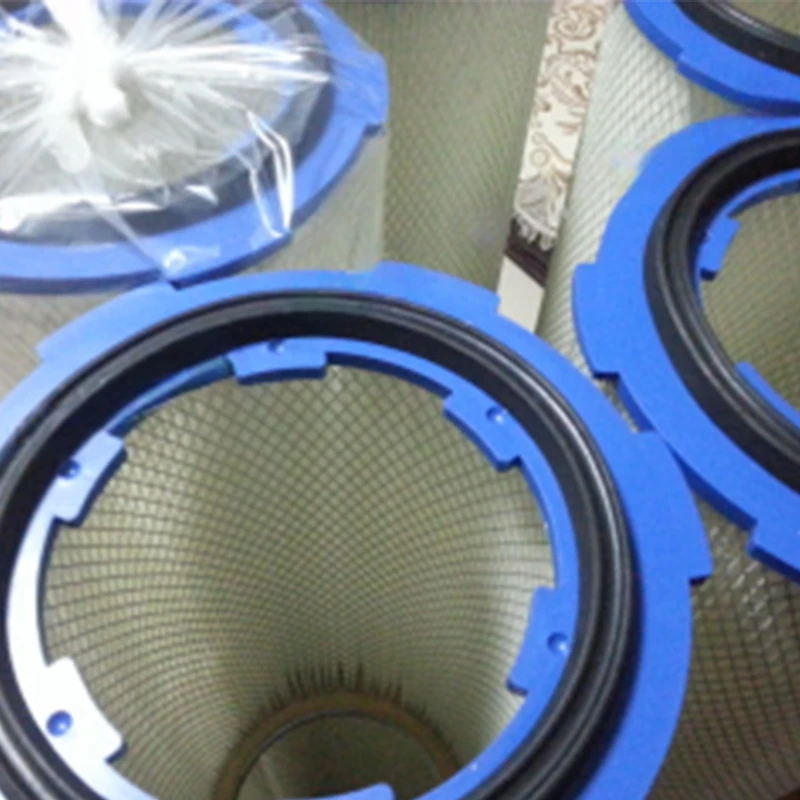
The wire mesh filter element's appeal lies in its intricate weaving of metallic threads, usually made from stainless steel, that form a robust filtration medium. This structure not only ensures longevity under high-pressure conditions but also enables precise particle retention. The inherent strength of stainless steel means these filters resist corrosion, high temperatures, and mechanical stress, making them suitable for demanding environments.
One of the standout features of wire mesh filter elements is their ability to be customized. Depending on the specific application requirements, the mesh can be tailored to facilitate different levels of filtration. From coarse filtration, eliminating larger particulates, to fine filtration for microparticles, the adaptability of wire mesh filters ensures optimal performance no matter the industrial need. This flexibility is crucial for operations requiring exact filtration specifications to maintain product integrity and efficiency.
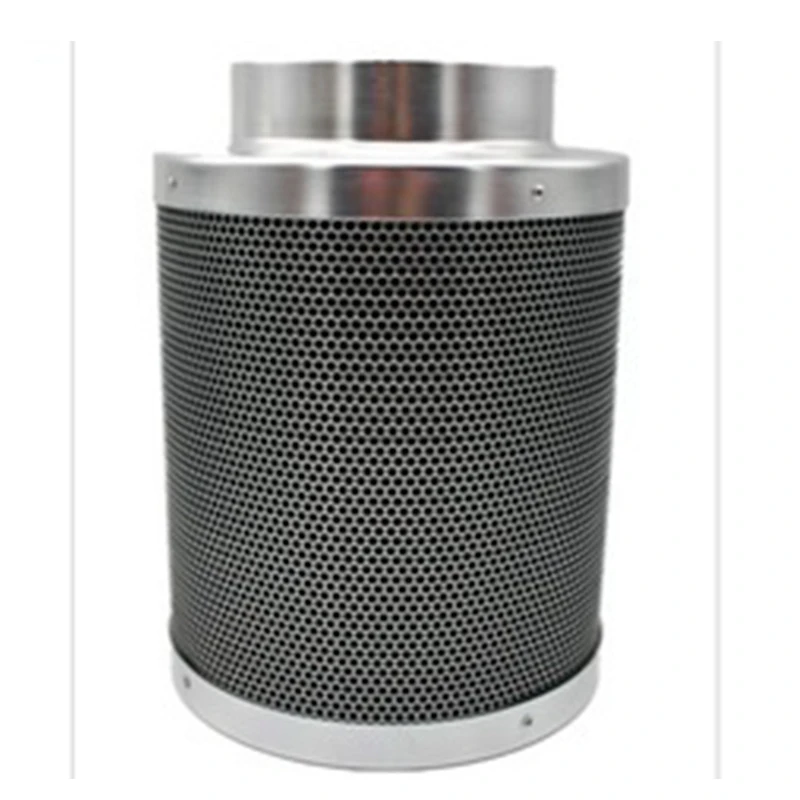
In the realm of petrochemicals,
wire mesh filters play a critical role. The industry demands filtration systems that can withstand aggressive media and high temperatures. The wire mesh filter elements, with their resistance to these harsh conditions, help in refining processes where precision is paramount. Similarly, pharmaceutical industries, where contamination control is crucial, benefit from the excellent filtration precision that these elements offer. They ensure that every batch's purity standards are met without compromise.
Automotive industries also leverage wire mesh filter elements for fluid systems, such as oil and fuel filters. These elements effectively prevent contaminants from damaging engines, thereby increasing the system's life span and reducing maintenance costs. In food and beverage processing, the health and safety regulations stipulate stringent filtration to prevent contamination. Wire mesh filters meet these standards by providing consistent filtration, ensuring that products are safe for consumption.
wire mesh filter element
What truly sets wire mesh filter elements apart is their reusability and ease of maintenance. Unlike disposable filters, these elements can be cleaned and reused multiple times, which significantly cuts down on replacement costs. The cleaning process, often through backwashing or other cleaning methods, restores their functionality effectively, making them not only a cost-efficient solution but also an environmentally friendly one.
It's essential to recognize the expertise required in manufacturing these elements. Precision in weaving the wires and ensuring the correct aperture size for specific applications takes significant skill. Manufacturers with a profound understanding of material science and engineering principles excel in delivering wire mesh filters that uphold the standards of Experience, Expertise, Authoritativeness, and Trustworthiness (E-E-A-T).
Furthermore, industry standards and certifications play a pivotal role in aligning these products with global regulations. Reputable manufacturers invest in certifications to bolster their credibility, giving users confidence that the wire mesh filters are tested and approved for their specific applications.
Choosing the right wire mesh filter involves considering the specific requirements of the intended application, such as the nature of the media being filtered, pressure conditions, and the required mesh size. Consulting with experts who have extensive experience in filtration technology is invaluable. This expert guidance helps in selecting a filtration solution that offers the perfect balance between performance, durability, and cost-effectiveness.
Wire mesh filter elements, with their unparalleled durability, adaptability, and precision, continue to shape the future of industrial filtration. Their ability to deliver consistently dependable performance across various rigorous applications makes them a cornerstone in maintaining and enhancing operational productivity. As industries evolve, the demand for these sophisticated filtration systems only underscores their indispensable role in modern technology and industrial processes.