The wire mesh filter element is an indispensable component in various industrial applications, ensuring precision filtration and protection across a multitude of systems. These filter elements, typically crafted from high-grade stainless steel, are lauded for their durability and robustness. Their ability to withstand extreme temperatures, pressures, and corrosive environments makes them an ideal choice for demanding operations.
Wire mesh filter elements serve as a barrier to contaminants, ensuring that only clean fluids pass through. It's a feature that is not only vital for efficiency but also for the longevity of machinery and systems.
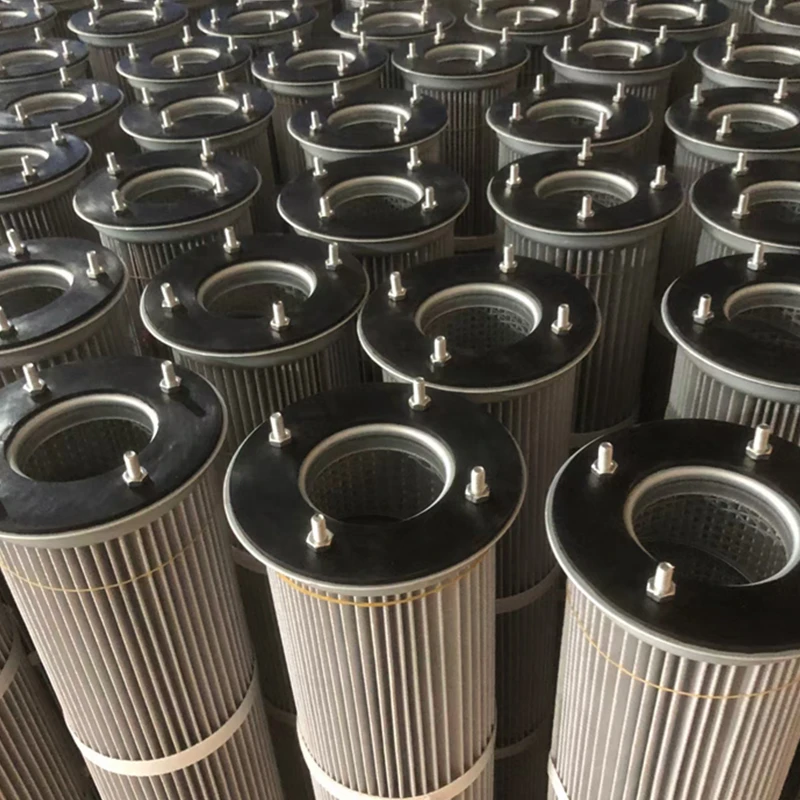
With decades of innovative design and manufacturing expertise, wire mesh filter elements have evolved significantly. Today, precision in their construction allows for tailored solutions across industries, from automotive and aerospace to food processing and pharmaceuticals. Companies rely heavily on these filters to maintain operational integrity and prevent machine downtime. The versatility of these filters, available in various shapes, sizes, and micron ratings, allows customization for specific applications, optimizing performance based on particular needs.
The expertise behind manufacturing these elements involves sophisticated weaving techniques that ensure a uniform structure. This uniformity is critical for maintaining consistent filtration levels. Expertise in metallurgy and engineering guarantees that each element meets rigorous industry standards. For instance, selecting the appropriate weave pattern - whether it be plain, twilled, or Dutch woven - can significantly influence the filter's performance, thus requiring a deep understanding of both the application requirements and the material characteristics.
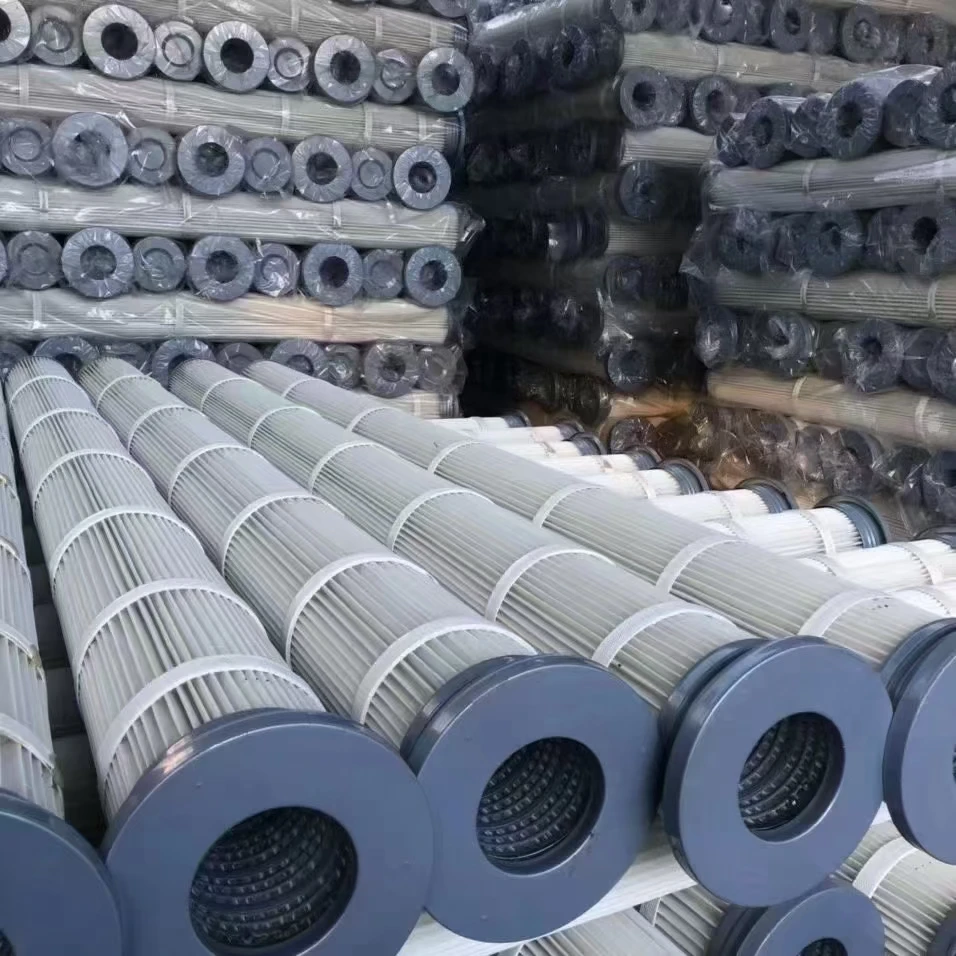
Authoritativeness in the field of wire mesh filter elements is established through extensive research, development, and testing. Leading manufacturers invest in continuous improvement, utilizing state-of-the-art technology to enhance product quality and reliability. This involves rigorous testing phases where filters are subjected to simulated operational conditions. Furthermore, collaboration with industry experts allows for the integration of feedback into the design process, ensuring that these elements meet the evolving needs of various sectors.
wire mesh filter element
Trustworthiness is paramount for manufacturers, as the reliability of wire mesh filter elements directly impacts critical operational processes. Transparent quality control processes and certifications from recognized bodies reinforce customer confidence. Manufacturers often provide comprehensive data sheets, detailing the specs, materials, and performance metrics, allowing engineers to make informed decisions when selecting filters. Moreover, excellent customer service and post-installation support help cultivate long-term trust and repeat business.
In practical terms, implementing wire mesh filter elements can lead to significant cost savings and efficiency improvements. By effectively removing contaminants, these filters help in decreasing wear and tear on equipment, reducing maintenance costs and extending equipment life spans. This is supported by real-world experiences from industries that report increased uptime and productivity, demonstrating the filter's contribution as a strategic component in operational workflow.
Overall, as industries continue to push the boundaries of technology and production capabilities, the significance of high-quality wire mesh filter elements cannot be overstated. They embody a blend of experience, expertise, authoritativeness, and trustworthiness, offering not only a product but a promise of unwavering quality and performance. By investing in superior wire mesh filter elements, companies assert their commitment to excellence and efficiency, ensuring that their systems run smoothly and reliably in even the most challenging environments.