Turbine filters, pivotal in ensuring the optimal performance of turbines, are not just functional components but an essential part of the turbine ecosystem requiring the highest expertise and reliability. When searching for high-quality turbine filters, it is crucial to delve into their construction, application, and maintenance, drawing on both technical insights and user experiences to make the best-informed decision.
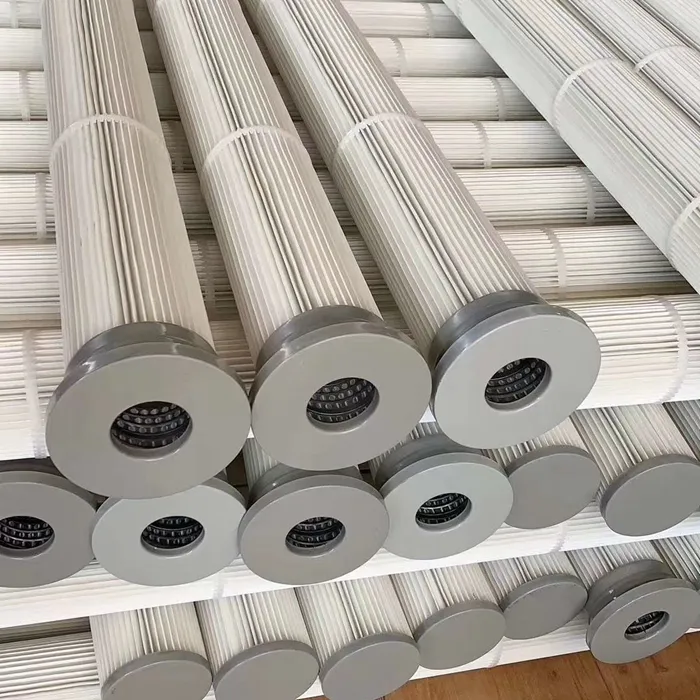
Turbine filters serve as the first line of defense against potential contaminants that can enter the turbine system, leading to inefficiencies or catastrophic failures. A turbine, whether it be used in power generation, aviation, oil and gas, or any industrial application, must maintain a high level of cleanliness to operate at peak efficiency. Turbine filters are designed to remove microscopic particles, dust, and moisture from the air intake system, preventing wear and tear on the machinery's components and ensuring longevity and optimal performance.
From an expertise viewpoint, the design of turbine filters is a science meticulously crafted to handle specific environmental conditions where turbines operate. The choice of materials—typically stainless steel, advanced polymers, and composite fibers—is critical to withstand temperature extremes, high pressure, and the corrosive nature of the operating environment. High-efficiency particulate air (HEPA) filters and ultra-low penetration air (ULPA) filters are commonly used in modern turbines, and they offer vastly superior filtration efficiencies, capturing particles as small as 0.3 microns.
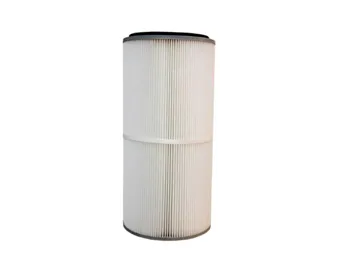
To maintain the authoritativeness of your turbine systems, understanding the various types of turbine filters is crucial. Primary and secondary filters, each serving a specific purpose within the filtration process, ensure comprehensive protection. The primary filter typically captures larger particles to prevent clogs and protect the finer secondary filter that deals with smaller, more intrusive particulates. Additionally, the use of activated carbon in some filters helps in eliminating harmful gases and odors, further safeguarding the turbine’s efficiency and the quality of air processed.
turbine filter
The experience shared by industry professionals underscores the importance of regular maintenance and timely replacement of turbine filters. Neglecting this aspect can result in increased operational costs due to higher fuel consumption and potential damage, which could incur significant repair costs.
As recommended by leading turbine manufacturers, filter replacement schedules are essential to maintain reliability and efficiency. Monitoring differential pressure across the filters will provide a clear indicator of when replacement is due, thus avoiding unnecessary downtime or damage.
When sourcing turbine filters, working with certified suppliers who provide documentation verifying the quality and compatibility of their products will establish trustworthiness in your purchase decisions. Certificates of compliance and validation reports should be regularly requested to ensure that the filters meet the industry standards such as ISO 29463 for the filtration of air.
A key takeaway for consumers and industry experts alike is the cost-benefit analysis that highlights the importance of investing in high-quality turbine filters. While initially more expensive, these filters generally provide better performance, extend the lifetime of turbine machinery, and reduce maintenance-related downtime, proving more economical in the long run.
In conclusion, turbine filters are an integral component of any turbine system, with the function of safeguarding efficiency and reducing operational risks. Leveraging comprehensive product knowledge, suppliers' expertise, and the recommendation of regular maintenance ensures that turbines operate seamlessly and efficiently. Always prioritize filters that promise quality, backed by professional recommendations and rigorous testing, to maintain a competitive edge in the industry and assure the durability and effectiveness of turbine operations.