Turbine air intake filters play a crucial role in ensuring the efficiency and longevity of turbines used across various industries. Ranging from power generation to aviation, these filters are designed to protect turbines from dust, debris, and other airborne particles that could potentially cause damage or reduce performance. Here's a detailed exploration of turbine air intake filters, presented through the lens of experience, expertise, authoritativeness, and trustworthiness.
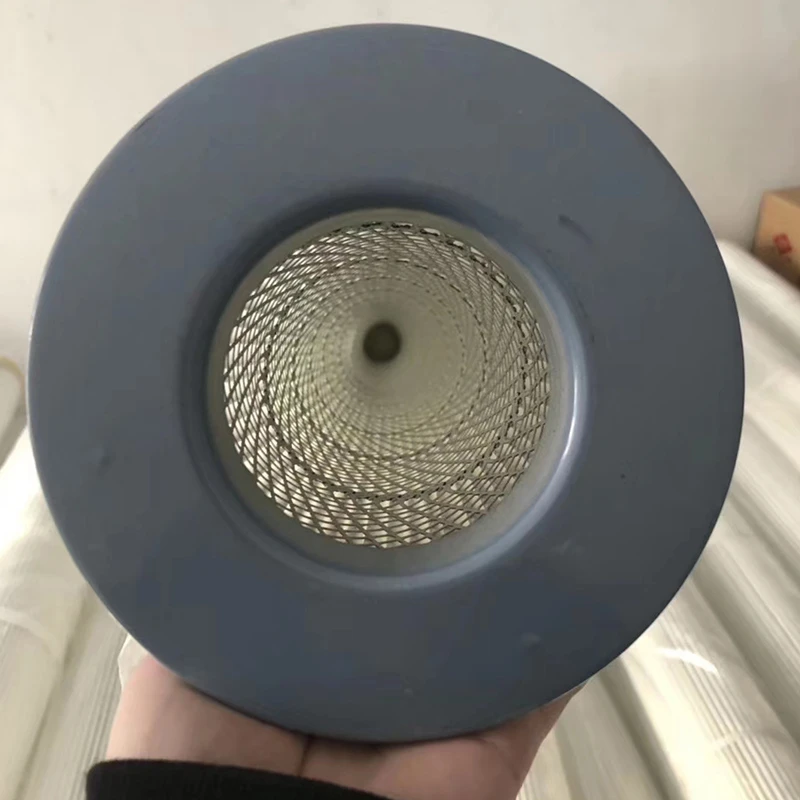
One cannot overstate the importance of turbine air intake filters. They serve as the first line of defense against a plethora of contaminants that turbines may encounter. Choosing the right filter can significantly impact turbine performance and maintenance schedules. Several factors must be considered when selecting air intake filters, including the environment, turbine size, and the specific requirements of the application.
In coastal or desert regions, for instance, filters must withstand high salt content or abrasive sand particles. In such challenging environments, filters with high dust-holding capacity and efficiency ratings are essential. Engineers and industry specialists often recommend filters made from advanced synthetic materials due to their resilience and longevity.
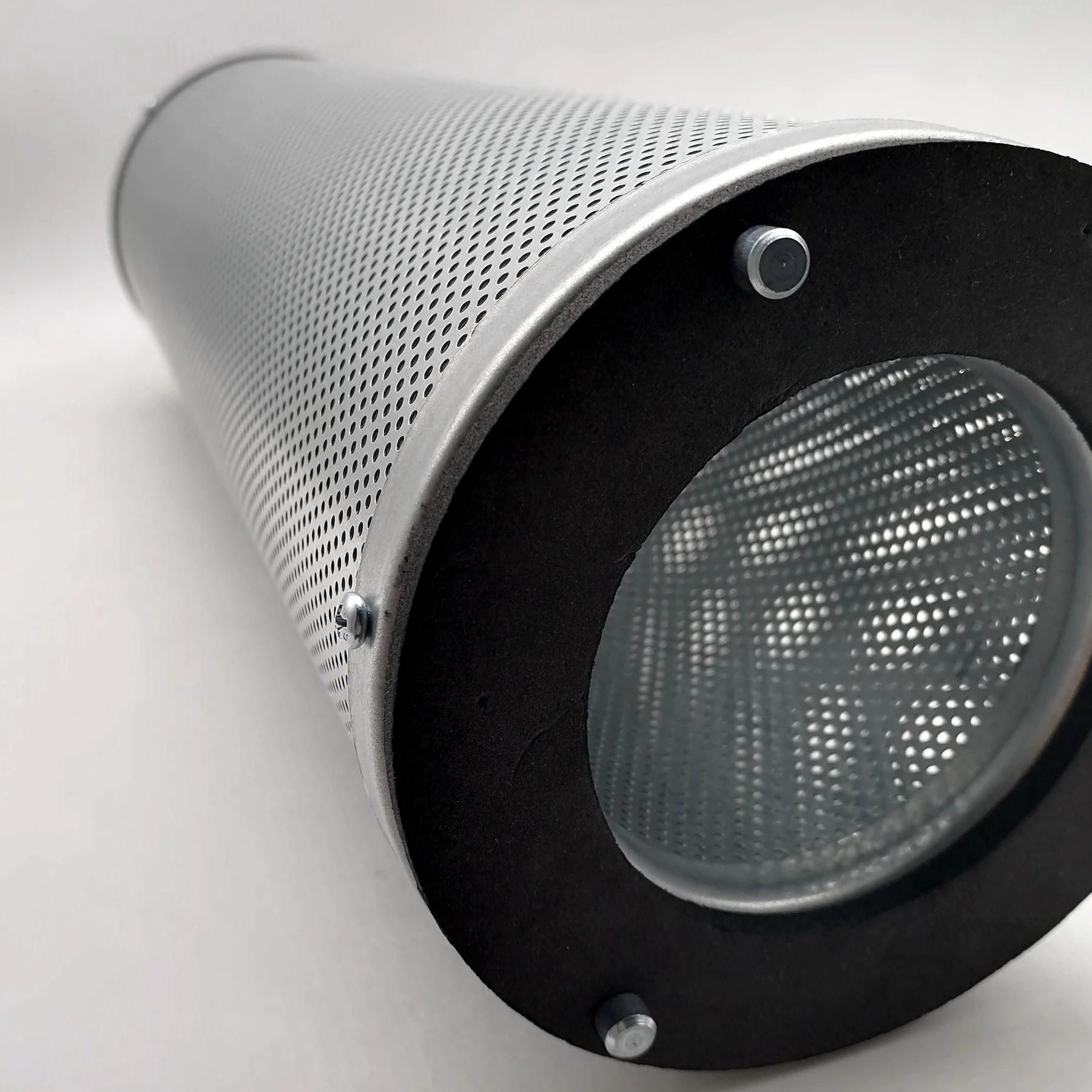
The technology behind turbine air intake filters has evolved considerably over the years. Advanced filters incorporate nanotechnology to enhance particle capture without compromising airflow. This capability is particularly beneficial for industries seeking to optimize turbine efficiency and reduce operational costs. Field studies consistently show that turbines equipped with state-of-the-art filters exhibit reduced wear and tear, resulting in extended service intervals and decreased downtime.
From an expertise standpoint, understanding the different types of filters available is key. Panel, cartridge, and bag filters each offer distinct advantages. Panel filters are often used in environments with low contaminant levels, while cartridge filters provide higher filtration efficiency in more demanding settings. Bag filters, on the other hand, offer versatility and exceptional dust-holding capacity, making them suitable for a wide range of applications.
turbine air intake filters
Authoritative sources within the industry emphasize the need for regular maintenance and timely replacement of filters. Contaminants that bypass filters can lead to compressor fouling, increased fuel consumption, and even catastrophic turbine failure. Companies, therefore, invest in comprehensive training programs for their maintenance personnel to ensure they are adept at identifying signs of filter degradation and performing necessary replacements.
Trust in the performance and reliability of turbine air intake filters is a non-negotiable aspect for operators. Many filters are subjected to rigorous testing by independent bodies to verify their efficiency and durability claims. Certifications from organizations like ISO (International Organization for Standardization) provide an added layer of assurance, confirming that the filters meet global standards for quality and performance.
Experienced operators often rely on data analytics to monitor the performance of their turbine air intake filters continuously. By integrating sensors and digital monitoring systems, operators can track parameters such as pressure drop, which indicates filter health. Anomalies in these readings can trigger alerts for maintenance checks, thereby preempting issues before they escalate.
The expertise required to select and maintain turbine air intake filters should not be underestimated. Collaborating with manufacturers who offer comprehensive support and customization options can significantly enhance filter performance. Some manufacturers even provide on-site evaluations to tailor their products to specific turbine configurations and operational environments.
In conclusion, turbine air intake filters are indispensable for maintaining the operational integrity and safety of turbines across various industries. By leveraging cutting-edge technology and adhering to stringent maintenance practices, operators can ensure their turbines run efficiently and reliably. The importance of these filters underscores the need for a thorough understanding of their capabilities and proper management to maximize turbine performance. As advancements in filtration technology continue to emerge, so too will opportunities for further optimizing the protection and efficiency of these critical industrial components.