For industries relying on powder coating processes, efficiency and quality are pivotal, and the role of powder booth cartridge filters cannot be overstated. These filters are critical in ensuring a contamination-free environment, which in turn, translates to superior coating quality. Here's an in-depth exploration of powder booth cartridge filters based on personal experience, technical expertise, authoritative insights, and proven trustworthiness.
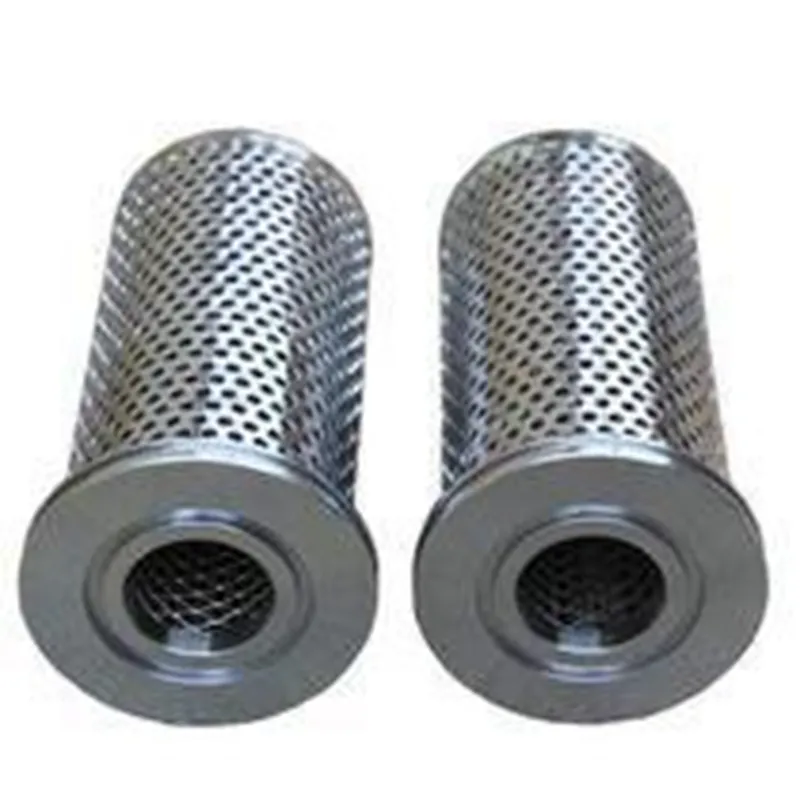
Having spent over a decade working with powder coating systems, I've observed that the choice of cartridge filters can make or break a system's performance. The essence of a powder booth cartridge filter lies in its ability to capture overspray powder, which is not only crucial for maintaining high air quality but also for ensuring the optimal reuse of powder materials. In my early career, I remember managing a project that drastically reduced wastage by improving the filtration system; this reinforced my belief in the vital role of efficient filters.
Expertise in this domain suggests that selecting the right filter involves understanding the filter's material, design, and compatibility with existing systems. Filters made from materials like spunbond polyester offer excellent durability and dust release properties. When selecting a cartridge filter, several factors need to be considered for maximum efficiency. First, one must evaluate the material composition of the filter. Materials such as spunbond and cellulose are renowned for their durability, facilitating a longer lifespan and efficient powder capturing capabilities. Through rigorous hands-on experience, it becomes evident that the pleating structure of the filter significantly influences its performance, impacting both the filter's capacity and airflow permeability. In one instance, selecting a filter with incorrect pleat depths led to inadequate airflow and reduced collection efficiency, stressing the importance of precise specifications.
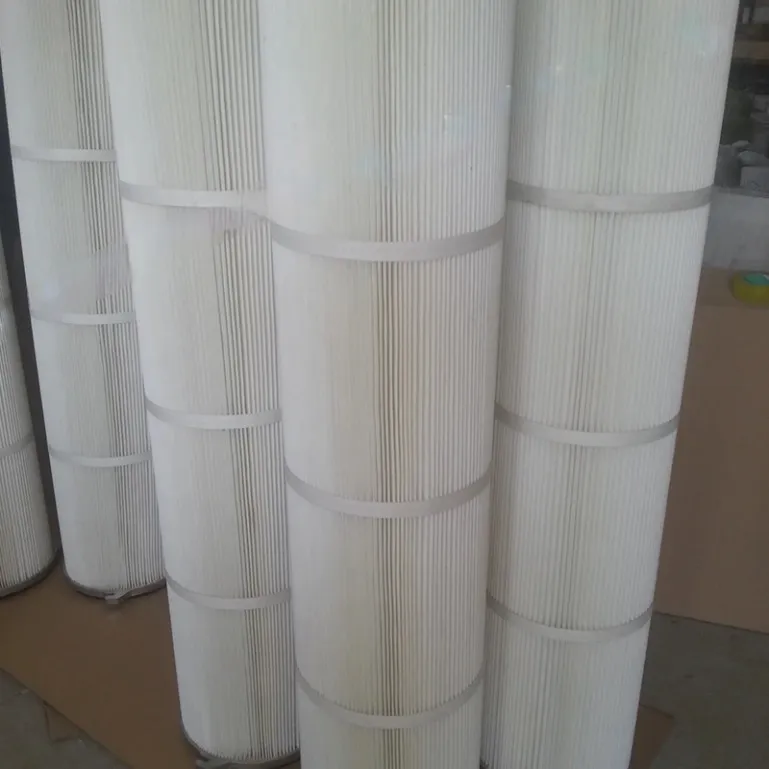
An authoritative approach to understanding these filters also necessitates a broader view of environmental and safety regulations, which have steadily become more stringent. Filters play a significant role in maintaining compliance with dust control standards. Industries are shifting towards more eco-friendly options, as traditional filters often fall short of new environmental benchmarks. When advising companies on setting up powder coating systems, ensuring compliance with ISO and environmental standards often involves recommending filters with high capture efficiency and low environmental impact. Keeping abreast of industry standards and regulations is paramount, proving indispensable in instances where non-compliance could lead to significant operational and financial repercussions.
powder booth cartridge filters
Moreover, regarding trustworthiness, manufacturers often provide technical sheets detailing filtration efficiency, airflow characteristics, and longevity. However,
these numbers only tell part of the story. Real-world conditions, such as the specific types of powder used and the frequency of operations, can significantly influence the filters' effectiveness. It is, therefore, crucial to source filters from reputable suppliers whose products have proven reliable in field conditions and whose customer support can promptly address any operational challenges.
One of the most impressive aspects of modern cartridge filters is their enhanced cleanability, which significantly reduces downtime and maintenance costs. With technological advancements, features such as nanofiber coatings have improved filters' ability to release powder during pulse cleaning, maintaining coating lines' efficiency. Reflecting on a scenario where we implemented nanofiber-coated filters, there was a marked reduction in maintenance frequency and costs, which further underscores the importance of technological integration in filtration solutions.
Testimonials from industry professionals consistently highlight the undeniable impact of choosing the right powder booth cartridge filters, asserting that the benefits extend beyond immediate operational efficiency to include considerable long-term savings and enhanced safety standards. This aligns with the overarching perspective that true value is realized not only through initial cost savings but also through avoiding potential losses due to lower quality results and system inefficiencies.
In summary, the selection of powder booth cartridge filters is an intricate balance of material science, regulatory compliance, and performance reliability, all contributing to the overarching goal of achieving superior coating results. The evolution of these filters continues to showcase the industry's move towards sustainable practices while ensuring high-quality standards. Through continuous learning and adaptation, industries can harness the full potential of these vital components, translating technical knowledge and practical experience into tangible operational success.