In the realm of drilling operations, the emphasis on maintaining peak operational efficiency cannot be overstated. A crucial component often overlooked is the air filter of a drilling rig. This critical element ensures that the machinery operates seamlessly and optimally, effectively preventing potential damages and maintaining the quality of the outputs. For those versed in the industry, the importance of a high-quality air filter is well-recognized, yet it sometimes remains underestimated among newer entrants.
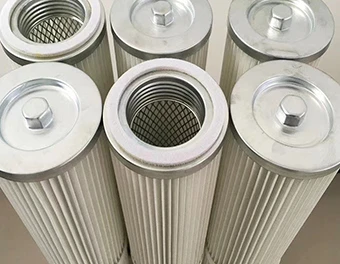
A drilling rig's air filter serves the essential function of cleansing the incoming air before it reaches the engine. By filtering out dust, debris, and other airborne contaminants, it effectively prevents these materials from entering the engine where they could cause significant damage. This proactive safeguarding extends the lifespan of the machinery, reduces maintenance costs, and ensures consistent performance.
Selecting the right air filter is paramount. An inadequately designed or substandard filter can lead to increased wear and tear on engine components, heightened fuel consumption, and a decline in overall drilling efficiency. It's crucial to choose an air filter that is specifically tailored for the rig's engine type and the environmental conditions it operates in. Filters constructed with multi-layered synthetic media tend to provide superior filtration efficiency and durability, catering to the rigorous demands of the drilling environment.
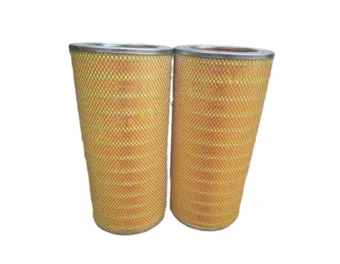
Routine maintenance and timely replacement of air filters are equally vital. An air filter clogged with dirt and debris can severely restrict airflow to the engine, leading to reduced performance and potential overheating. Thus, regular inspection and replacement should be integral components of an operator's maintenance schedule. Depending on the environment, air filters might require more frequent attention in areas with excessive dust or pollution.
An innovative approach that has seen increasing adoption is the integration of advanced sensors within air filtration systems. These sensors monitor the condition of the filter in real-time, alerting operators when a replacement is necessary. This technology not only enhances efficiency by predicting maintenance needs but also contributes to minimizing unexpected downtimes, which can be particularly costly in drilling operations.
drilling rig air filter
Furthermore, utilizing OEM (Original Equipment Manufacturer) parts for air filters is recommended to ensure compatibility and reliability. OEM products guarantee that the filter meets the specific design and performance criteria set by the manufacturer, thus ensuring optimal protection for the engine.
The impact of a well-maintained air filter system extends beyond equipment longevity and fuel savings. It also plays a role in the environmental considerations of drilling projects. Efficient filtration systems contribute to reducing emissions, aligning operations with regulatory standards, and supporting sustainability goals. This is of growing importance as industries worldwide pivot towards more environmentally conscious strategies.
Ultimately, the expertise and authority required to make informed decisions about drilling rig air filters stem from a deep understanding of their role within the broader context of drilling operations. Combining practical experience with innovation, professionals in the field are equipped to harness cutting-edge technologies to enhance both efficiency and sustainability. Trusting in high-quality components and adhering to stringent maintenance routines, companies can safeguard their investments, ensuring consistent performance and compliance with evolving industry standards.
The dynamic landscape of drilling operations necessitates ongoing adaptation and informed decision-making. As environmental concerns rise and technology advances, the evolution of air filtration systems will undoubtedly continue, necessitating vigilance and expertise across industry sectors.